Digital twins: enabling sale of a service, not an asset
Published on 14th June 2022
Digital twins are increasingly used in industrial systems. They can be transformative, enabling optimisation of efficiency and output. They can also shift the entire business model for a supplier from selling an asset to selling the service provided by the asset. The contractual relationship between supplier and customer shifts from the sale of goods to the provision of a service, becoming a much closer and potentially more enduring arrangement.
This is chapter 2.6 of Data-driven business models: The role of legal teams in delivering success
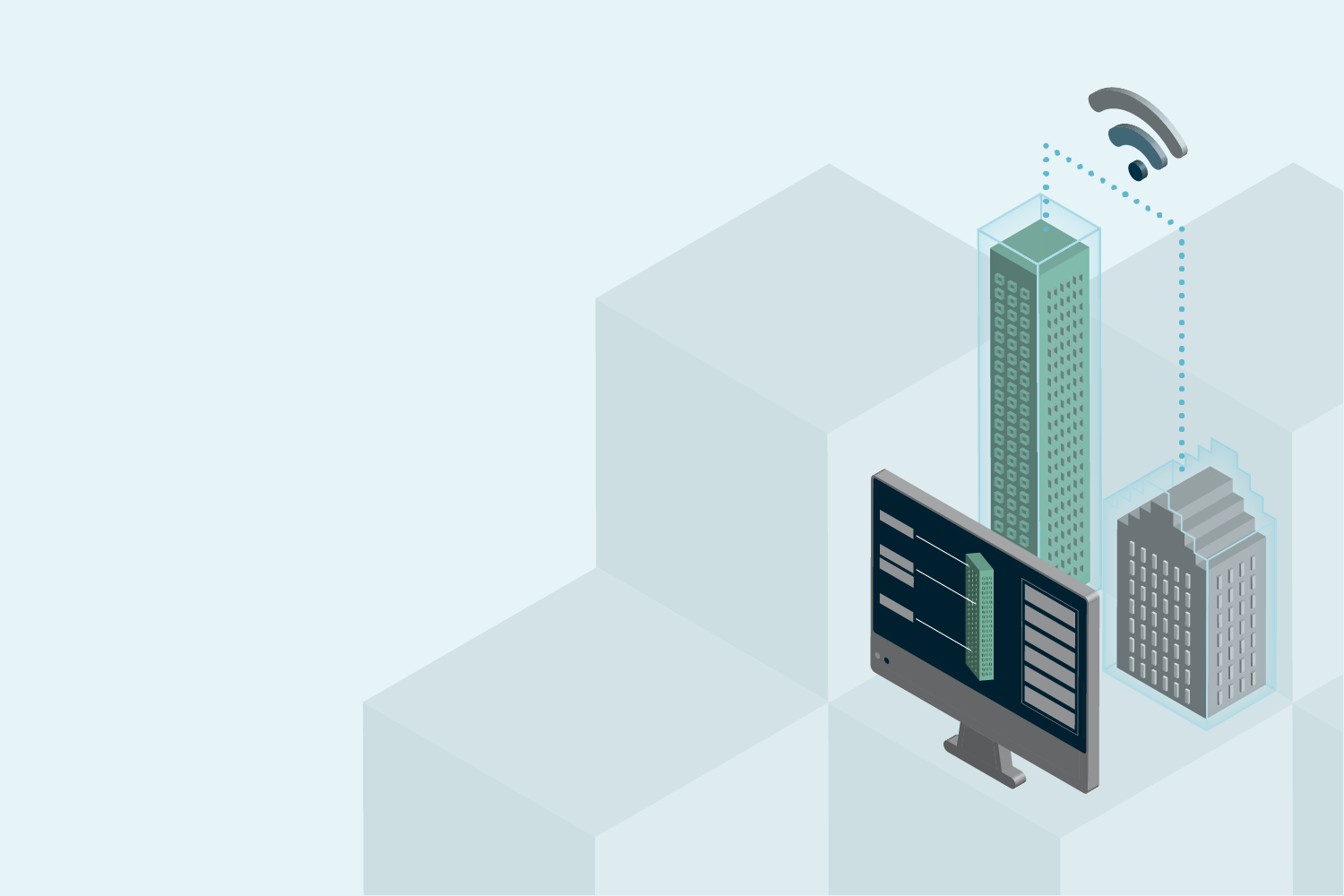
Key Takeaways
|
What is a digital twin?
Digital twins use connectivity, Internet of Things (IoT) technology and data flows to turn a straightforward digital model of something physical into a virtual mirror of not only its shape but also its movement, the processes that it undertakes, how it performs, and associated data such as consumption of inputs and production of outputs. Data flows between the physical and digital versions of the asset keep them synchronised. Performance of the physical asset can be mapped onto the virtual one, facilitating real time or slower analysis and optimisation.
In themselves, digital twins can be transformative, particularly in manufacturing, processing and (as discussed in Chapter 2.8) in the built environment. But they are also enabling a fundamental shift in how assets are supplied to customers, supporting data-driven 'Assets as a Service' business models and the 'servitisation' of the provision of physical goods – i.e. selling the service provided by the asset, rather than the asset itself.
Digital twins in industry systems
Digital twin applications
In industry, processing and manufacturing, digital twins are an advanced application of digital technology – sometimes called 'Industry 4.0'. Anything from single machines, to individual production lines or whole factories can be digitally modelled and connected to create their virtual mirror.
Digital twins are typically hosted in the cloud and so can be accessed and controlled from anywhere. Where a digital twin sends and receives data to and from the physical twin with real time data flows, it can be used to monitor or control the physical asset remotely. Real time digital twins can be used as an early warning system for problems with machinery or infrastructure. They can be integrated with augmented reality tools to enable visualisation of the data flows and information about output and performance against each piece of machinery as someone walks the factory floor. Digital twins can also integrate with additive manufacturing systems (industrial 3D printing), enabling the manufacture of bespoke repairs based on the digital model and insights into the malfunctioning parts.
Alternatively a digital twin can be run separately to the physical twin. Such systems might be used for training purposes, for example to teach repair or maintenance routines for remote or dangerous assets such as wind turbines. Financial risk can be considerably reduced by building, testing and finessing a prototype as a digital twin before any expenditure or investment is made in building a physical prototype. When the physical prototype is built, it is much less likely to need radical modifications. When the new product is ready for production at scale, its digital twin is already in place.
New hardware or software can be tested and commissioned on a digital twin, rather than the physical machinery. Performance can be tested and optimised on the digital twin. Once perfected, the finely tuned improvements can be transferred across to the physical machinery with minimal disruption to production schedules. Historical data about performance can be analysed to understand patterns of wear and tear or asset failure, enabling predictive maintenance and more efficient deployment of maintenance staff, and correspondingly reducing unexpected downtime and emergency call-outs.
For all of these reasons, digital twins are increasingly an integral part of software systems for industry and manufacturing.
![]() Data-driven business modelsThe role of legal teams in delivering success |
Legal issues
Digital twins typically need collaboration with a number of providers.
Most smaller businesses will procure the core technology from an external source. Many of the traditional industrial engineering conglomerates have transformed themselves into digital industry specialists, turning their in-house technical expertise into third party offerings and new revenue streams. Cloud-based hosting services may be provided by that business or a third party. Building the digital twin, installing the new systems and establishing the data flows may well need consultancy services from the software provider or another specialist. Depending on the sophistication of the twin,
collaboration may be needed with research bodies (for example, the digital twin might include scientific data about the physical properties of its moving parts such as friction or vibrations).
All of these relationships will need to be documented and shaped with procurement and/or consultancy agreements. Depending on the complexity, value and degree of customisation of the systems being installed, these projects can require bespoke negotiation of contractual relationships.
In particular, care will be needed to define responsibilities and liability. These will often become ongoing commercial relationships once the initial development and installation is complete, and may become business-critical, particularly if production depends on them. For that reason, expertise in tech dispute resolution can be essential if such relationships break down at any point – replacing technology systems can be extremely disruptive. It may be sensible to agree up front provisions to deal with below-par service or performance to minimise disruption should disputes arise.
It may also be sensible to consider enhanced cybersecurity provisions across these relationships. Digital connections into third parties constitute a new avenue of attack and cyber risk. Agreeing key performance indicators for cyber and information security management from suppliers is recommended, backed up with periodic reporting requirements and audit rights.
Digital twins powering assets as a service
The 'servitisation' model
Digital twins of an asset can power an even greater transformation where they enable a manufacturer or supplier to switch from selling the asset itself to selling the service that it offers.
This model is used across a range of valuable assets, from aircraft engines sold on the basis of the power delivered, to packaging machinery at the end of a production line sold on the basis of the number of wraps made. The asset is installed with the customer – at their premises, on their production line or on their aircraft – but title over the asset does not pass to them and remains with the supplier.
Pricing is based on the service provided: a price per use is multiplied by the number of times the customer uses the asset. The price can be bundled to include repairs and servicing of the asset, additional consumables or an allowance for spare parts. Insurance may well remain the responsibility of the supplier, in which case it becomes part of the cost base for providing the service.
A bundled pricing structure often lends itself to a subscription model with a fixed price per day, week or month, based on projected use or consumption over that period. Digital twins enable a different approach. Very granular pricing can be calculated based on actual operation of the physical asset, monitored by data flows back to its digital twin. The data enables the supplier to issue invoices for the exact amount of the service
that has been consumed by the customer.
For the customer, this can be a powerful shift, particularly where the asset concerned is of high value. In particular, it transforms what would have been capital investment in acquiring the asset into operating expenditure that is a variable cost driven by actual consumption. No asset finance is needed to procure the asset; it will not appear on the balance sheet; there will be no depreciation charges; and, overall, there will be reduced financial risk. This change flows into corresponding differences in tax treatment of the asset and the service provided by it.
Legal issues
At its most basic, the shift from selling an asset to selling the functionality that it offers changes the legal relationship between supplier and customer from a contract for the sale of goods to an agreement for the provision of services.
In particular, the relationship between supplier and customer moves from being primarily a relatively time-limited interaction of ordering, delivering and perhaps installing the asset, to a closer relationship over a much longer period. Performance of the ongoing interaction between supplier and customer becomes more significant. Key performance indicators will need to be agreed – both what to measure and how to measure it. They may be needed in relation to both the output of the asset and associated services such as repairs and maintenance. It could be prudent to anticipate how any disputes should be dealt with, to minimise as far as possible the risk of any escalation of disputes in a relationship which may be business-critical, for example for maintaining production output levels.
The digital twin of the supplied asset will be the property of, and/or controlled by the supplier (at least as far as the customer is concerned). If the customer is to have access to the digital twin for the asset and/or access to the data collected from the asset, terms and conditions around data flows and associated digital services will need to be agreed. Cyber and information security provisions may also need to be included. To the extent that the digital connections between the parties create risk for each other, the parties may wish to include cybersecurity performance levels in the agreement, which might be reinforced by agreed audit and reporting processes.
Given the industrial context, the data protection regime for personal data is not likely to be in play. However, the customer may wish to include confidentiality or ringfencing provisions in relation to data collected by the supplier's digital twin, since it may provide valuable insight into its business's performance. It may also wish to constrain any wider use of data flowing from its use of the asset by the supplier.
A clear liability framework will need to be agreed between the parties to ensure that responsibility for any issues such as breakdowns, faulty operation, problems with the data flows or functioning of the digital twin is clearly allocated. If the day-to-day operation of the asset is carried out by the customer's staff, the supplier may require the customer's staff to undergo specified training to ensure that the asset is used correctly. Allocation of liability between the parties will need to include where the asset is damaged or underperforms due to errors by the customer's staff, or the damage is otherwise caused by them.
As regards pricing, the supplier will need to consider whether the costs of installation are charged up front, or recouped during the lifetime of the contract as part of the cost base for the services supplied. If the latter, would a pro rata penalty for early termination be needed to recoup upfront costs that had not yet been clawed back? Terms of renewal will need to consider how the absence of installation costs affects pricing for the second contractual term, as well as any adjustments for changes in other costs. Although concerns tend to be less acute in relation to business-to-business relationships, fairness in pricing where contracts roll over into new terms has been a focus for competition and consumer authorities.
On termination, ongoing access for the customer to historic data collected by the supplier about the performance and output of the installed asset will need to be considered, as well as arrangements for timely recovery of the asset by the supplier.
As regards financing the asset, this will no longer be needed by the customer. Any asset finance will instead be needed by the supplier, perhaps to fund manufacture of the new asset, to be serviced by the future revenue stream from the customer. Potentially, the need to service debt may necessitate a minimum purchase obligation on the customer to ensure that a lower level of use of the asset by the customer than forecast does not create risk of default by the supplier under the financing arrangements.
As with any commercial relationship, the extent to which the supplier is prepared to negotiate its standard terms and conditions around the supply of an asset provided on an 'as a service' will depend on the value of the contract and of the wider commercial relationship with the customer. The larger the installed asset base of the supplier, the less it will want different terms of service provision with different customer
Future regulation of IoT data flows
At present, there is minimal regulation around non-personal data flows. The performance of machinery is unlikely to reveal information about identifiable individuals so data privacy regulation will not usually be a prime consideration in relation to an industrial digital twin or a servitisation business model.
However, the European Commission's recent proposals for a Data Act would extend the scope of data regulation to include swathes of non-personal data generated in a business context.
Manufacturers of data-collecting connected products and providers of related services will be required to make the data generated by their use easily accessible to the user, whether a business or a consumer, potentially in real time as it is collected. The user will be entitled to pass the data on to third parties or use it for their own purposes. Users may also demand that the data is made available directly to third parties. The manufacturer or supplier's own use of that data will be limited and need to be contractually agreed with the user.
The Data Act, which is intended to reshape the European data ecosystem, is discussed in more detail in Chapter 2.10. It remains some way off from becoming law, and is expected to be changed as it makes its way through the legislative process. But it is extremely likely that the ability to comply with the new regime – including the capability to pipe data out to users and third parties – will need to be designed into all new data-collecting business models, and retrofitted into existing ones. Digital industrial systems will be no exception.