Are modern methods of construction in the UK more sustainable?
Published on 27th April 2023
Can modern methods of construction, such as off-site manufacturing, help to reduce carbon emissions generated in the construction of new buildings?
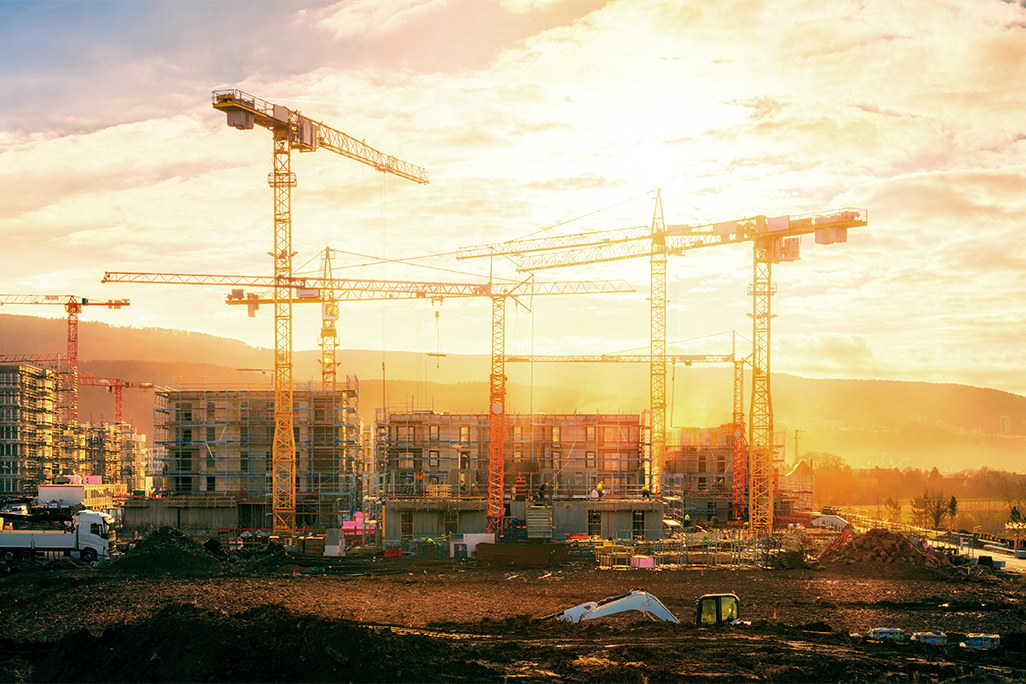
According to a 2022 report from the Environmental Audit Committee, the built environment is currently responsible for 25% of total UK greenhouse gas emissions. These emissions can be broken down into two main categories: operational carbon and embodied carbon.
Operational carbon refers to the emissions generated across the operational lifetime of buildings. Embodied carbon refers to the emissions associated with materials and construction processes throughout the whole lifecycle of a building.
In recent years, much of the industry's focus has been on reducing operational carbon by making buildings more energy efficient. However, recent research (including that carried out by the Carbon Project, a decarbonisation initiative of the Institute of Civil Engineers) has demonstrated that, while operational carbon emissions within the built environment have been falling over the past decade, embodied carbon has conversely increased. Accordingly, a shift in focus within the industry towards tackling the problem of embodied carbon is beginning.
Using modern methods of construction (MMC) to complete a project is often touted as one way in which that project can improve its sustainability credentials. But are MMC technologies actually more sustainable than more traditional methods of construction?
What is MMC?
MMC is an overarching term used to describe a range of techniques which aim to maximise the use and benefits of manufacturing in construction processes.
One of the most widely used forms of MMC in the UK is off-site manufacturing (OSM), where certain aspects of the final project (such as pre-fabricated units) are manufactured off-site, and delivered to the construction site for incorporation into the project. OSM includes a number of forms of construction, including modular construction (also referred to as volumetric construction) or panelised units, for example precast concrete facade panels.
There are a number of advantages to using MMC, including an improved speed of construction, greater predictability of programme and improved quality of the finished product (see our earlier Insight).
While MMC is far from being a new concept within the UK construction industry, its use has been steadily increasing. It is also now central to the government's construction playbook which sets out the guidelines for the procurement and delivery of government projects.
How can MMC reduce embodied carbon?
A 2013 report by Building Intellect found that MMC can reduce embodied carbon in a number of ways, including via:
- Reduced traffic movements, with fewer deliveries to site.
- Reduction in build time and energy use on site, with fewer person-hours on site requiring less energy for heating and lighting for staff welfare and less plant and equipment use.
- Reduced levels of waste.
- Increased levels of versatility, as MMC can be used alongside technologies such as 3D printing and built-in sensors to help monitor the performance of the product (including detecting any defects early on) thereby increasing the lifespan of the products/builds.
Recent research
A recent joint study between Cambridge University and Edinburgh Napier University, commissioned by modular manufacturer Tide Construction, found that modular construction did reduce overall embodied carbon emissions. The study was based on assessing the embodied carbon of two modular buildings: a high rise (44 storey) residential scheme and a mid-rise (10 storey) residential scheme. The study found that the embodied carbon of the 44 and 10 storey modular schemes was 40% and 54% lower (respectively) than the RIBA & Leti Carbon Benchmarks.
Other research has elicited similar results. A study in South Korea of a six storey residential building found that modular construction reduced embodied carbon by 36% when compared against a traditional reinforced concrete frame building.
However, studies into certain other MMC methods (not OSM) have led to some different conclusions. A 2022 study published by Liverpool University found that the embodied carbon created by a two storey house built using a panelised system was 2.3 times higher than an equivalent house built using traditional methods. These findings suggest that not all MMC methods achieve carbon reductions on all projects, and may in some instances lead to an increase in embodied carbon.
The differing outcomes suggest that the carbon reduction credentials of MMC are, to some extent, dependant on what percentage of the construction will actually be carried out off-site. OSM can potentially allow for a large percentage of the construction process to take place off-site. Panelised systems, on the other hand, still require installation of the panels on-site, followed by fit-out. This greater on-site activity has the knock-on effect of higher embodied carbon relating to road traffic, energy used on-site and greater volumes of waste, therefore somewhat limiting the decarbonisation benefits of MMC.
However, in light of technological advances, this position is far from static. A recent project from the UK Green Building Council developed a solution that reduces the embodied carbon in precast panels by up to 40% against the industry baseline. This solution is now being rolled out across the £2 billion prison building programme for the Ministry of Justice. This suggests that there is scope for precast panels to deliver the same reductions in embodied carbon as OSM.
Should I use MMC on my project?
MMC technologies have the potential to deliver significant benefits on suitable projects in terms of carbon savings and also in terms of improved quality and time savings. They are not, however, a silver bullet, and the suitability of MMC technologies on a particular project needs to be carefully considered.
Some practical drawbacks of using MMC include a limited scope in initial design and for late design changes. There can be challenges when installing modules on constrained sites. There are also important financial and legal considerations that need to be factored in to any decision around utilising MMC technologies.
For example, MMC usually requires significant payments to be made by developers in respect of goods which are being manufactured offsite. Developers will need to consider how best to protect any such advance payments, and how best to assert ownership of any goods while they remain off-site.
Procurement structures should also be carefully considered in order to ensure that off-site manufacturers are engaged on appropriate contract terms early on in the life of the project.
Osborne Clarke comment
Current research suggests that MMC, particularly in the form of modular construction, provides a viable means of achieving potentially significant reductions in embodied carbon.
Although it cannot currently be said that all methods of MMC can provide embodied carbon savings, the ongoing research into the ways in which embodied carbon can be reduced (given its sizeable contribution to current emissions) is likely to lead to continued advances in the sustainability credentials of MMC.
Despite the potential role of modular construction in helping the built environment to reach net zero targets, the current market is showing some signs of strain. The fairly recent collapse of Caledonian Modular and modular housing joint venture House by Urban Splash are clear examples of the challenges in the market.
While the construction industry is generally facing pressures as a result of high levels of inflation, other factors, such as a lack of demand for MMC products, can lead to a challenging market for MMC manufacturers. In an industry with relatively low margins and where project pipelines can be uncertain, investment into MMC is often put on the back-burner and therefore the industry may only see a significant uptake in MMC (and any resulting carbon reduction benefits) when there are higher volumes of demand, resulting in a somewhat "chicken and egg" scenario. The outlook is by no means consistently bleak, with plenty of success stories for long-term MMC market operators showing more positive signs for the future of modular manufacturing in the UK. But in the short to medium term we expect some further pinch points for MMC, particularly as inflation is likely to continue at relatively high levels and as we wait to see what comes first in our chicken and egg analogy.
In considering whether to use MMC on a particular project, developers need to be aware of the limitations of MMC, particularly with regard to the design of a building, and restrictions on any amendments to that design. Legal advice should also be sought alongside technical guidance in order to ensure that the particular risks associated with MMC are adequately addressed. If these limitations can be overcome, we may see an uptake in off-site construction in the coming years as the construction industry and its clients look to reduce their emissions in order to contribute towards net zero goals.
Osborne Clarke Senior Associate, Jonathan Culley, will be speaking about the key legal considerations to enable the increased uptake of MMC in construction on 15 June 2023 at the Construction News Decarbonising Construction 2023 conference.
This article was written with the assistance of David Herron, trainee solicitor.